System integrators (SIs) often have a hard time enabling communications among the different platforms in a network. At the heart of the problem is the large variety of protocols in the three divergent domains of network architecture: Operation Technology (OT), Information Technology (IT), and the Industrial Internet of Things (IIoT). Each domain comes with its own set of protocols that effectively creates non-interoperable silos, making it impossible for useful data to reach those who need it on an enterprise level to make important decisions. Matters are further complicated by the fact that both the OT and IT departments are unfamiliar with the protocols used in each other’s domains. Clearly, these two departments cannot afford to work in isolation from each other anymore, because as the IIoT makes inroads into automation, OT and IT technologies are converging.
OT-to-OT Interoperability
Since the advent of the IIoT, OT-to-OT communications in factories have become much more complicated due to the large number of sensors and machines connected to the Internet. The result of this growing complexity of operations processes is more heterogeneous systems on the factory floor. The heterogeneous systems that fall under OT—such as manufacturing executive systems (MESs), supervisory control and data acquisition (SCADA) systems, programmable logic controllers (PLCs), and the machines and sensors on the plant floor—all run their own protocols; consequently, non-interoperability becomes an issue and a multitude of protocol conversions are required.
For SIs, this means that installation and setup require more time to plan the architecture and perform device commissioning. But SIs don’t want to spend long hours on device commissioning and configuration, or on protocol conversions. They want an easy way to simplify protocol conversions so that they can spend their limited time on their core tasks, such as programming.
To accomplish the mass configurations of devices and protocol conversions between different devices, a ready-to-use protocol gateway that supports the multiple industrial protocols commonly used in OT, such as PROFINET, PROFIBUS, Ethernet/IP, and Modbus, is the best solution. This type of gateway simplifies protocol conversions, resulting in significant cost- and time-savings.

OT-to-IT Interoperability
Close cooperation between the IT and OT departments is essential to tap the full potential of any smart application’s IIoT platform. IT departments face an increasing demand to collect data from shop floors in order to optimize production. For IT staff, this is not an easy task as they are not familiar with the process of collecting data via industrial protocols. Concurrently, OT staff members face a similar predicament when they transfer OT data to the IT layer, because IT departments often request protocols they are not familiar with.
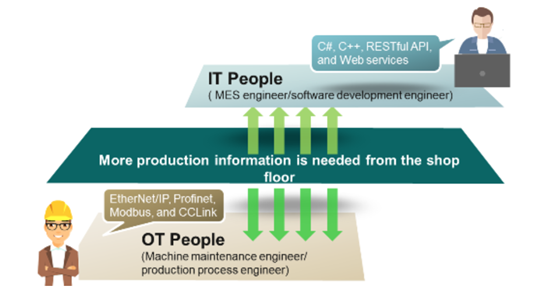
To bridge this great divide between OT and IT, a smart I/O that supports various protocols (such as Modbus/TCP and Ethernet/IP for industrial automation (IA) engineers, and SNMP and RESTful API for IT engineers) is necessary This solution makes it possible for both IT and IA engineers to conveniently retrieve data from the same I/O device.
OT-to-IIoT Interoperability
The overall goals for data mining and analytics are to reduce operation costs, optimize production, and enhance predictive maintenance to minimize downtime. First, data needs to be collected from field sites and then transferred to the cloud, where it is stored for analytics purposes. And it has become the job of OT engineers to transfer this data from the field to the cloud. Undoubtedly, this new addition to their job description takes OT engineers out of their comfort zone due to their lack of IT knowledge. Sending data from an edge device to the cloud can be time-consuming, and OT engineers’ unfamiliarity with IT technology only compounds the process.
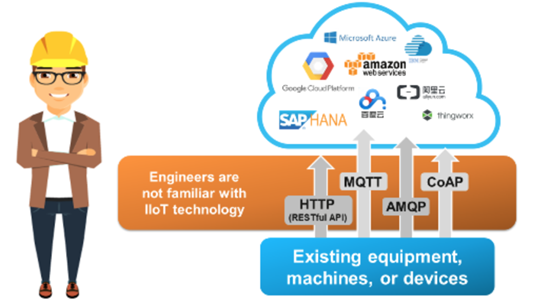
To spare engineers lots of programming effort and to reduce time and costs, an embedded computing platform that supports versatile interfaces, coupled with a software suite that integrates a ready-to-use Modbus engine and cloud connections such as AWS, enables fast integration between devices in the field and the applications required for the IIoT. Furthermore, for those who want to adopt OPC US in order to unify automation interfaces, a software suite solution is available that provides both an OPC UA server as well as cloud connection capabilities. A further benefit of this solution is that it requires no extra costs to implement additional architecture for cloud connectivity.
Moxa's Solutions
For more information about Moxa’s comprehensive portfolio of solutions to make interoperability smoother in factory automation, visit our website here.