The emergence of the Industrial Internet of Things (IIoT) has changed the way the Operational Technology (OT) world uses data tremendously. In the past, data was simply collected for monitoring purposes to ensure production goes according to schedule. Now, data can go beyond a mere stream of information. Through analysis, data not only can help optimize products and services, but can also significantly improve operational efficiency, increase profits, and create new business models that previously were not possible. The vast business opportunities presented by data have made the IIoT a key technology for the future success of nearly all businesses.
The benefits presented by this shift have triggered a demand for machines that cater to data acquisition and analysis, anywhere and everywhere possible. Previously, companies valued only production data, which monitors the productivity of machines or assets to ensure smooth operations. Nowadays, along with production data, machine condition data is just as crucial. Enterprises depend heavily on the predictive analysis of real-time operational data to prevent potential failures in order to reduce maintenance cost and the risk of other possible damages. Furthermore, industrial equipment manufacturers can use the historical data of machines to provide customers with more accurate and faster maintenance services to reduce personnel costs. Lastly, this data can be used to optimize a machine’s operation based on environmental and business objectives that require dynamic updates and changes as opposed to the historical “set-and-forget-it” mentality.
Despite the considerable benefits of big data, the advancement of the IIoT in the industrial space is still slow. The hindering factors are multiple: the variety of edge protocols, nonstandardized data, connectivity to the cloud, cybersecurity, the management of large-scale systems, to name a few.
The Two Most Common IIoT Connectivity Solutions
In the early days of the IIoT (as recent as two or three years ago), industrial equipment manufacturers’ answer to this complex and challenging problem was to provide a turnkey IIoT solution. The customer only needed to pay for this service or feature, and the equipment vendor would take care of the rest. As time went on, customers quickly found themselves stuck with multiple IIoT solutions from different vendors on different platforms, with little to no interoperability. What’s more, they were missing the big picture that all of their collected information supposedly was to reveal. Everything was in silos from different vendors.
As customers came to grips with this challenge, market demand called for open architectures that offered customers the option to take charge of and maintain their own IIoT strategy, allowing them to talk to any device in any location. However, the issue remains complex with regard to the investment and capabilities required to pull this off at scale. Most customers, even those with will well-intended and well-funded solutions, face tremendous challenges building such a type of solution.
Let’s take a closer look at the two common connectivity methods: proprietary IIoT connectivity solutions that offer an easy and managed approach but with constraints on flexibility, openness, and data ownership, and open IIoT connectivity solutions that focus on the cross-systematic integration of any device and the end customer’s ownership of the solution.
Proprietary IIoT Connectivity Solutions: Easy, Hassle-free Solutions
A number of industrial equipment manufacturers saw the value that came with data analytics, and began to provide customers with their own IIoT connectivity solution. To leverage the wealth of data, IIoT gateways are installed in front of or embedded in the “thing”, and data regarding the status of the “thing” will be transmitted from the machine to the machine vendor’s cloud. This user-friendly turnkey solution allows customers to quickly capture, manage, visualize, and analyze the data collected from these devices on a cloud-based platform. This system is fairly intuitive for users as they only need to log into the machine vendor’s cloud to access their data. It further reduces a customer’s workload by placing the burden of developing and deploying the system solely on the industrial equipment manufacturer, effectively lowering the overall IT cost for the customer.
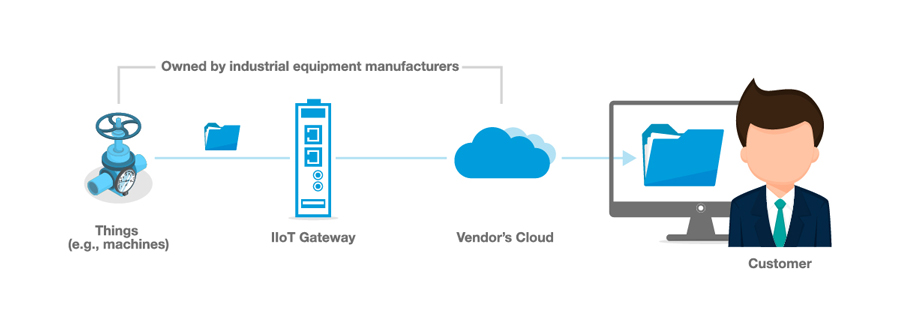
(Fig.1. A proprietary IIoT connectivity solution)
A few industrial equipment manufacturers also began to provide data analysis services on top of the data collection offering to help customers better understand their machines’ behavior. This offering is favored by customers with specific application needs, such as monitoring the operations of remote equipment. In the case of the oil and gas industry, punctual operation of remote devices (pumps, control valves, compressors, etc.) is top priority. This has prompted industrial equipment manufacturers, such as Baker Hughes, Emerson, Schlumberger, etc., to start using artificial intelligence (AI) to perform real-time analysis of data, such as pump pressure, flow, temperature, etc. Coupling this data with past benchmarks, they can promptly adjust the equipment parameters to keep them operating normally with minimal human intervention. Thus, proprietary IIoT connectivity solutions’ hassle-free deployment and easy-to-use features have made them very popular among customers.
Hassle-free, But at What Cost?
This easy-to-deploy solution’s homogeneous nature means that its service is limited to the industrial equipment manufacturers’ own devices. However, in reality, a medium-sized enterprise usually has equipment and assets from multiple vendors, in multiple locations, spanning many different applications. This complex, heterogeneous environment often requires the enterprise to use a different solution for each system provided by a different industrial equipment manufacturer. This could quickly result in extra financial investments, not to mention the possible obstacles arising from the isolated information systems that cannot speak to each other.
- Inflexible Integration: Within closed IIoT solutions, the data is sent to different platforms, with each using different protocols and different formats, creating a colossal effort at the backend to merge the data.
- Lack of Data Ownership: Since the customer's machine data is stored on a private platform built by the industrial equipment manufacturer, data ownership becomes an issue. If the data is stored in a system owned by the builder, does it still belong to the customer? Furthermore, if a customer chooses to switch platforms one day, the risk of incomplete data transportation—if not all together impossible—is huge. This could potentially cause the historical data and past experiences accumulated by the customer to be lost. All of this, coupled with the risk of a data leak, point out a glaring obstacle in the solution.
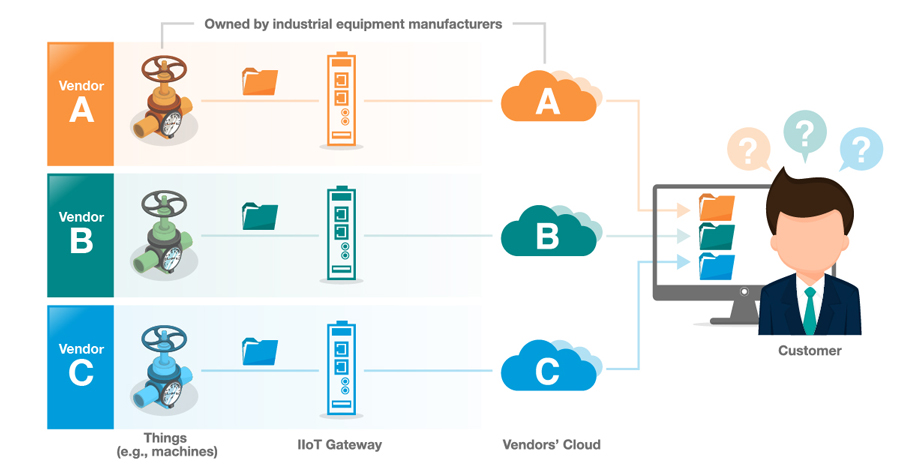
(Fig.2. Connecting multiple things in a proprietary IIoT connectivity solution)
Is Openness the Answer When Connecting Multiple “Things”?
As data starts to play a more significant role in a business’ core success, its ownership, availability from all “things” (not just some), and the flexibility of integration are the main considerations when choosing solutions.
In open IIoT connectivity architectures, industrial equipment manufacturers open APIs or use open or standard-based protocols to help customers obtain the data by themselves. Contrarily, sometimes customers build their own solutions by connecting individual front-end equipment from different manufacturers to a highly integrated IIoT gateway. The different data formats from the different manufacturers are unified by the IIoT gateway, thus significantly reducing the integration difficulties when data is subsequently transmitted to the cloud. In addition, the process no longer requires the data to be passed through a third-party's platform, making it more secure.
Take the oil and gas industry as an example. Oil production and real-time oil prices are closely linked, which means transparency in the production line can make or break the profit margin. In order to gain real-time data from exploration, development, and production to final transportation, oil companies partnered to create an open platform. This called for the industrial equipment manufacturers in the supply chain to work as a team by sharing their equipment, production, or environmental data for the efficient production of an oil field.
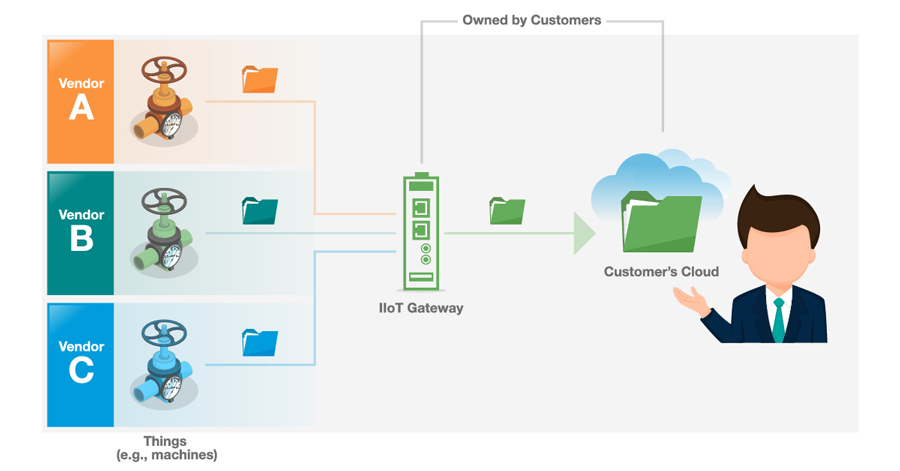
(Fig.3. An open IIoT connectivity solution)
Now, the question quickly becomes “What can I buy?” versus “What do I have to build by myself?” The commercial available solutions today for open architectures have expanded rapidly over the last 12 months. Various software components are now available to accomplish this:
- Cloud Edge Software such as AWS IoT Greengrass/Azure IoT Edge to extend cloud infrastructure to the edge
- SCADA Edge Software such as Ignition Edge/AVEVA Edge IoT View to interface a vast variety of industrial edge protocols
- Infrastructure service offerings to extend security, networking, and management to the edge such as ZEDEDA, OpenVPN, and TOSIBOX Lock for Container
- ML/AI edge solutions for edge processing before pushing back to the cloud
Most importantly, don’t forget to choose a powerful yet reliable IIoT gateway at the core, which not only can run the above software components, but also has the ability to connect to the cloud (e.g., LTE, Wi-Fi, existing WAN) and edge (e.g., I/O, Ethernet, USB, Serial, other).
Conclusion: Proprietary or Open?
For companies that want to deploy a quick IIoT solution for a singular vendor’s, “thing” to obtain data and reap the benefits of the IIoT, an easy-to-deploy, proprietary IIoT connectivity solution is the more rewarding choice. For companies that require IIoT data on a larger scale, are interfacing many different “things”, and are looking for a more personalized fit with full data ownership, an open IIoT connectivity solution would be able to deliver the necessary optimization.
As the IIoT market and IIoT ecosystem evolve, more off-the-shelf software and cloud products, without a doubt, will continue to provide customers easier and highly scalable products to build their own open IIoT solution. Proprietary IIoT solutions are also having to adapt quickly to provide more open API’s and cloud-to-cloud integration, as well as open up their solution for customers to access their data more easily.
To learn more about IIoT gateways for your proprietary or open solutions, click here.