In industrial applications, data is worth gold. And, it is exactly the accelerated drive industry-wide to acquire and analyze volumes of raw data that is shaping the Industrial Internet of Things (IIoT) as we know it today. One area where the influence of the IIoT is significantly felt is in the collection of I/O data from field devices. Increasingly, the IIoT requires networks to push collected I/O data to OT (private cloud) and IT (public cloud) platforms for analysis purposes. Commonly, modular remote I/Os are used to retrieve I/O data. Unfortunately, they come with a few pain points that not only frustrate engineers, but also impact daily operation. In this article, we take a closer look at these pain points and discuss a solution that will appeal to OT and IT people alike.
The Reality of Reconfiguration Bites
For modular remote I/O setups, one of the greatest difficulties is duplicating configuration settings to the current modules with different module combinations. After adding, moving, or deleting one of the modules, configuration of the unchanged modules, including the Modbus address and RESTful APIs to the upper software, need to be redone. Ideally, system integrators want to keep all the completed settings between the devices and upper software, and only configure the newly added modules with minimum effort involved.
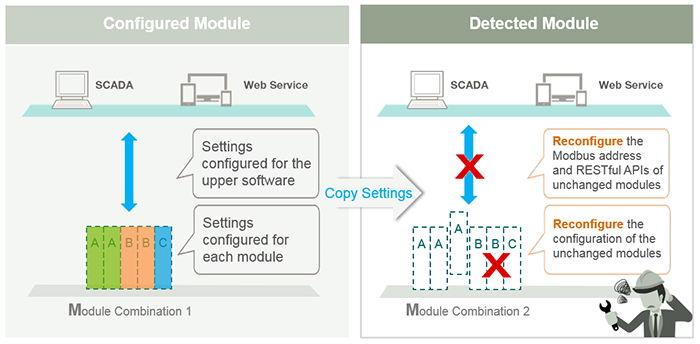
But the reality for system integrators involves long hours and repetitive reconfigurations when dealing with different module combinations in different sites. Let’s say, for example, that the module combinations in Site A, Site B, and Site C are AABBC, AAABBC, and AACBB, respectively. Duplicating the configuration settings of the I/O modules in Site A to those in Sites B and C is not so straightforward. In site B, an extra module (in the figure, represented by A) has been added. So, the SI not only needs to configure the newly added module, but also needs to reconfigure modules B, B, and C. The same frustrating scenario applies to Site C where a module has been removed and replaced by another (in this case C). Here, module C needs to be configured from scratch, and the two modules identified as B reconfigured. To the chagrin of system integrators, just adding, deleting, or moving a single module involves a lot of extra effort. Therefore, eliminating reconfiguration in the duplication of configuration settings will save a lot of time and money.
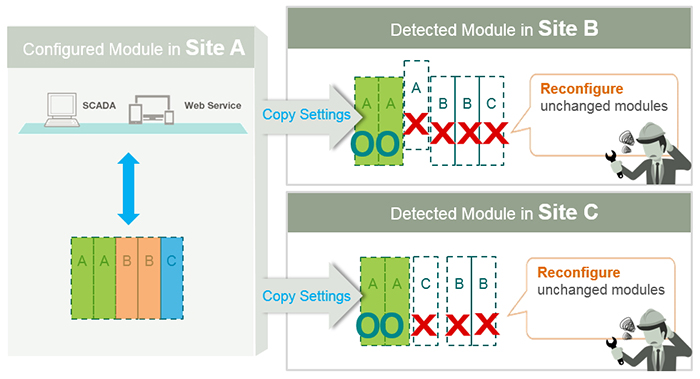
The Right Protocols Matter
Modular remote I/Os can also be an annoyance when it comes to protocol support. Many modular remote I/Os in the market do not support the IT protocols, such as SNMP and RESTful, with which many engineers are familiar with. So engineers have to spend more time and effort to complete their project as the modular remote I/O only supports OT protocols. Finding a solution that supports multiple OT and IT protocols in one device makes a world of difference.
Moxa’s Solutions
Our ioThinx 4510 is designed with an intuitive web configuration tool that supports module/channel unique name. Simply put, the configuration settings, including Modbus address/RESTful channel name to SCADA, will correspond automatically with the specific module. Additional reconfiguration efforts are not required no matter whether you change the module sequence, add, or remove a module. You just need to configure only the newly added module.
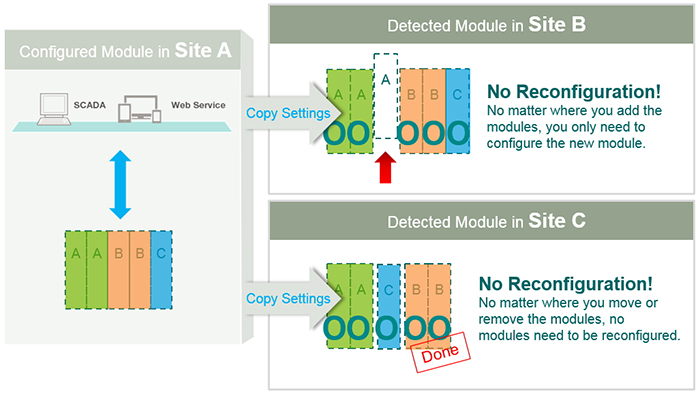
Furthermore, the ioThinx 4510 speaks several different protocols, including Modbus TCP for OT engineers, as well as SNMP and RESTful API for IT engineers. The ioThinx 4510 retrieves I/O data and converts the data to any of these protocols, allowing you to get your applications connected easily and effortlessly.
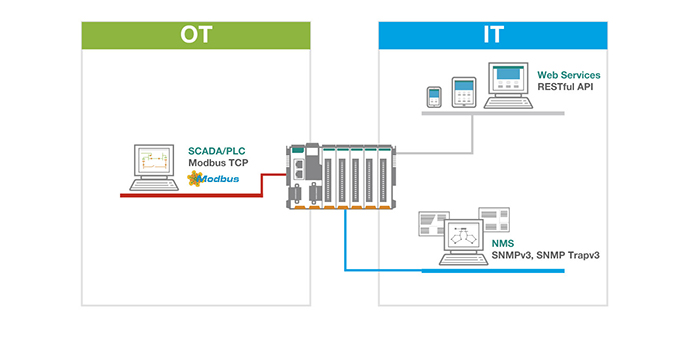
For more information, visit our microsite.