The impact the Internet has had on the way humans live their lives has been unprecedented. It has allowed us to communicate and interact with each other in ways previously unimaginable. Recently, it has opened the door for what many are describing as something that will become more important to our everyday lives than the Internet, the Internet of Things (IoT).
One of the most exciting possibilities is in industrial applications, more commonly referred to as the Industrial Internet of Things (Industrial IoT), where communication and interaction capabilities can be extended to devices or Things, such as factory automation, renewable energy, smart grids, intelligent transportation systems, and even oil and gas applications. Strategy Analytics released a report last year that predicted machine-to-machine connections will grow from 368 million in 2015 to 2.1 billion by 2022. No one doubts that the potential of the Industrial IoT is enormous. However, before these statistics and the full potential of it become visible in our everyday lives, there are several issues that need to be addressed.
In Industrial IoT environments, it is very common for several devices to share the same network, but it is often the case that different devices support different communications protocols. For the Industrial IoT to be truly valuable, the diverse devices that are deployed must be able to share information and communicate freely. As it currently stands, data is harvested from devices and sent to the central server. Depending on the size of the application, anywhere from several up to hundreds of thousands of devices could be involved. Then, the server has to process the device data so that people can make data-informed decisions. The problem of different devices using different communication protocols can be overcome by companies writing their own programs to ensure that their devices can communicate with each other. However, taking into consideration that this is a complex and costly integration procedure that could prolong the installation process, this is not an ideal choice for smart companies.
With the possibilities that the Industrial IoT presents, we must not lose sight of its ultimate purpose, which is to make users’ lives easier. As Brown University Computer Scientist Michael Littman has pointed out: If users need to learn different interfaces for their vacuums, their locks, their sprinklers, their lights, and their coffeemakers, it’s tough to say that their lives have been made any easier.
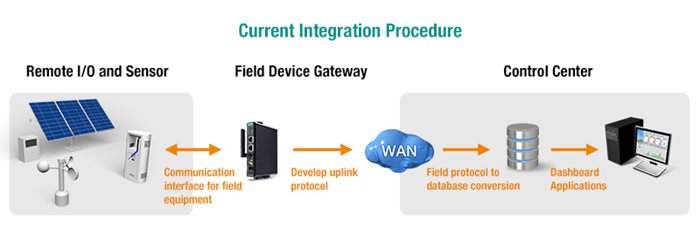
Since an Industrial IoT environment is comprised of several areas, each of which requires a different type of expertise, engineers from a wide range of backgrounds are needed to handle projects efficiently. For example, many people in the automation industry are knowledgeable about industrial protocols such as Modbus, but they are not familiar with Information Technology and 4G LTE. Conversely, many people in the IT industry are familiar with communication technology but not with industrial protocols. This problem often presents companies with two scenarios:
- Spend a significant amount of money on their current engineers to train them how to operate devices they are not currently familiar with.
- Acquire new talent to fill the areas currently lacking professional knowledge and expertise.
More and more developers in Industrial IoT environments have noticed the aforementioned problems when building Industrial IoT infrastructures. It cannot be underestimated how important it is to overcome these problems in order to implement successful Industrial IoT deployments and how critical any technology is that can help reduce costs.
First, in order to solve businesses’ pain points and allow them to successfully develop and deploy their Industrial IoT applications, the diverse devices must be able to share information and interact freely. Second, engineers working with protocols they haven’t previously worked with or in applications where they don’t have specialized knowledge is an issue that must also be addressed in order for the Industrial IoT to reach its full potential. In short, helping businesses save costs and get their products to market quicker is going to be of paramount importance for any Industrial IoT environment.
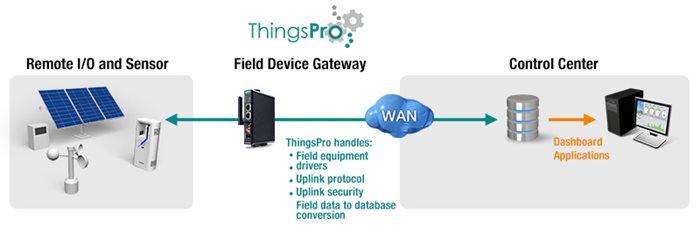
Moxa has been involved in many Industrial IoT project installations over the past few years, so we are aware of the challenges businesses have been facing for some time. One of the solutions we developed is a software suite, called ThingsPro, that helps businesses address these issues. ThingsPro is installed on a field gateway, such as Moxa’s UC-8100 series, and its primary function is to collect data from field devices and then convert the data into a format that can communicate with the central server and database.
ThingsPro currently has two utilities, Data Logger and Wireless Manager, that solve compatibility issues between different protocols as well as reduce engineer’s work load during installations. Data Logger converts the information from different end devices so the information can be sent to the database, and in turn produces information that can be used by the business. Wireless Manager assists people who are familiar with automation technology in connecting their field devices to a WAN by conducting the conversion work for them. The result is that it is not necessary for engineers to spend extra effort to become familiar with wireless connectivity technology so they can focus more on the data collected from the devices and data analysis, which is the ultimate goal of an Industrial IoT project. The advantage of this approach will in turn allow businesses to deploy their equipment faster, complete the project quicker and overall to develop a more effective solution.
As Industrial IoT environments continue to expand rapidly, the demand for the ThingsPro Software Suite is also increasing because of its ability to assist businesses in bringing their solutions to market quicker by functioning as a wireless manager for people unfamiliar with ICT protocols and as a data logger for people unfamiliar with automation technology. Additionally, in comparison to other solutions, it offers a much lower total cost of ownership. One of the main reasons for this is because the Gateway has a built-in cellular module, which with the support of ThingsPro allows it to function as a wireless router and perform the data logger functions that would normally be performed by a computer. Thus, users do not have to purchase a separate computer and wireless router, which significantly reduces costs.
Furthermore, to adapt various Modbus devices, the Modbus template can be reused to add additional Modbus devices without the user needing to program the configurations again. The existing gateway configuration and template settings can also be imported/exported allowing for faster deployment via the GUI. Finally, the user can also perform troubleshooting and maintain the system’s historical log files through ThingsPro. For more information about ThingsPro and the Industrial IoT in general, please visit this site.