Performance is king in networks across the board. After all, it is the key measure of any operation’s success. Not surprisingly, the drive for maximized performance goes hand in hand with rapid changes and technical advances. It is also no secret that these changes place Industrial Internet of Things (IIoT) technologies at the heart of a wave of innovation in network connectivity and infrastructure.
As expected, with new opportunities come new challenges as well. These challenges may vary from industry to industry, but the crucial issue that constantly comes to the fore is the need to build reliable networks that enable higher productivity and better energy efficiency. The fact that system requirements vary from project to project further complicates the issue since a one-size-fits-all solution that can be applied to different network infrastructures does not exist. The bottom line, however, is that system integrators need to guarantee that their networks, especially those used for mission-critical applications, can withstand connection failures and adverse environmental conditions.
In this article, we consider three feasible strategies for ensuring that factory automation networks provide reliable, nonstop connectivity.
Networks that Create Value for Factory Automation
According to a McKinsey Global Institute report, IIoT applications in operations optimization are expected to create value of US$633 billion to $1.8 trillion per year in the factory sector by the year 2025. After operations optimization, the next most valuable applications of IIoT in factory automation are predictive maintenance and inventory optimization. But before these values can be unlocked, the industry needs to overcome the following challenges:
Interoperability
For IIoT applications to be adopted in a factory setting, network interoperability is the most complex issue given that a factory usually comprises a large number of complex systems and applications. Improvement in interoperability is required for both machine-to-machine communications and for relaying large streams of data from the production floor.
.png)
Strategy: To increase productivity and reduce operating costs, plant operators opt either for industrial Ethernet gateways or multiprotocol-capable switches, instead of embedded computers, to converge isolated fieldbus systems for centralized control and monitoring. Gateways and multiprotocol switches are cost-effective and easy-to deploy. Also, they not only increase collaboration between various systems, but also optimize PLC performance and manageability.
Reliability
Busy and noisy manufacturing environments can impact network reliability. Given that a factory network infrastructure includes many networking devices, network reliability depends on device durability, network redundancy, and cybersecurity capabilities.
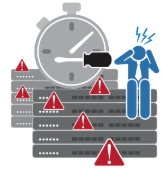
Strategy: Network devices such as Ethernet switches, wireless devices, and secure routers must be designed to endure extreme temperature variations, shocks, vibrations, EMI, and other harsh conditions. Activating a backup connection as soon as a network failure occurs is essential to ensure network resilience, regardless of whether your network uses a multicast or unicast scenario. VPNs, routers, and NAT protection are necessary for mission-critical devices and communication, and Modbus deep-packet inspection is a plus for factory-floor communication.
Systems Integration
SCADA and information network systems are usually parallel platforms, and for IIoT applications, integrating SCADA systems with information network systems will become more and more crucial.
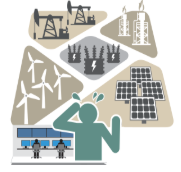
Strategy: Instead of using parallel SCADA and IT management systems, advanced industrial-grade network management systems can act as an OPC server to keep SCADA systems informed about network status, and graphical user interfaces can give engineers intuitive network visibility for faster configuration and VLAN management. Also, mobile apps are now indispensable for instant network monitoring, even while on the move.
Data is front and center in the IIoT world of connected devices. The strategies discussed here for interoperability, reliability and the integration of systems will make it possible for data to be moved from the edge of a network to a control center for extracting valuable information.
To learn how to implement smart information sharing throughout your plant for better productivity and energy efficiency, visit our website on smart factory networks. Also, check out this FAQ with five important questions to ask before implementing the IIoT.